Upgrading Fischer-Tropsch (FT) waxes through catalytic hydrocracking and isomerization is essential for producing high-quality transport fuels. Hydrocracking operates efficiently under mild conditions, creating valuable diesel with fewer contaminants. Meanwhile, selective hydroisomerization enhances lubricant base oil properties. Both methods improve fuel quality and economic viability, aligning with today's demand for cleaner energy sources. If you stick around, you might discover even more innovative techniques and benefits involved in this upgrading process.
Key Takeaways
- Upgrading Fischer-Tropsch (FT) waxes through hydrocracking produces high-quality diesel fuel with improved conversion efficiency and economic viability.
- Hydrocracking operates under mild conditions, resulting in high-quality diesel free from sulfur and nitrogen contaminants.
- Selective hydroisomerization enhances lubricant properties by altering paraffin structures, producing superior quality lubricant base oils.
- Incorporating FT waxes in fluid catalytic cracking (FCC) feeds increases conversion rates and reduces coke formation, enhancing overall process efficiency.
- The resulting light cycle oil (LCO) from FCC shows improved properties, aligning with market demands for lower aromatic content.
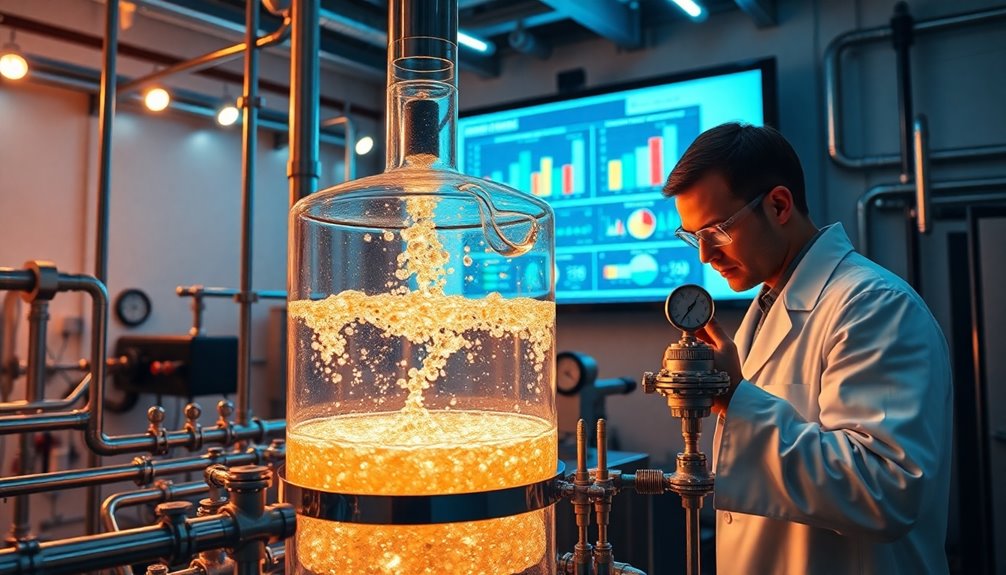
As the demand for cleaner transport fuels rises, upgrading Fischer-Tropsch (FT) waxes has become a crucial focus in the energy sector. You're likely aware that FT waxes, derived from the Fischer-Tropsch synthesis, require upgrading to transform them into usable transport fuels like diesel and gasoline. This process typically involves hydrocracking and selective hydroisomerization, both of which enhance the quality and usability of these waxes.
Hydrocracking stands out for its high conversion efficiency, transforming FT waxes into liquid fuels under mild operating conditions. This method benefits from the absence of sulfur or nitrogen contaminants, resulting in high-quality diesel fuel with satisfactory catalyst performance. Operating typically at pressures of 3.5-7 MPa and temperatures between 597-645 K, hydrocracking is economically viable due to the quality of the resulting fuels and lower processing conditions. Additionally, the incorporation of FTS wax in feedstocks has been shown to improve the yield of middle distillate fractions during catalytic processes.
Hydrocracking efficiently converts FT waxes into high-quality diesel fuel under mild conditions, enhancing economic viability and catalyst performance.
On the other hand, selective hydroisomerization plays a vital role in producing high-quality lubricant base oils. By altering the paraffin structure, this method improves lubricant properties significantly. The catalysts used in this process require specific acidity levels to achieve optimal performance. Despite its complexity, selective isomerization offers advantages over conventional methods, yielding lubricants with superior characteristics.
You might also find it interesting that catalytic upgrading techniques like Fluid Catalytic Cracking (FCC) can convert FT waxes into lighter products such as light cycle oil (LCO). Adding FT waxes to FCC feeds not only increases conversion rates but also reduces coke formation, enhancing overall process efficiency.
The light cycle oil produced shows improved properties, including lower aromatic content, which is a significant plus in today's market.
Frequently Asked Questions
What Are Fischer-Tropsch Waxes Used for Besides Fuel Production?
Fischer-Tropsch waxes have diverse applications beyond fuel production.
You can use them as lubricants in PVC processing, improving efficiency and surface gloss. They also enhance pigment dispersion in coatings and paints, ensuring a smooth finish.
In the adhesive industry, they're ideal for hot melt adhesives due to their heat resistance.
Additionally, these waxes contribute to candle making, rubber protection, and even improve the texture of textiles, showcasing their versatility.
How Does Catalytic Hydrocracking Differ From Other Refining Processes?
They say, "You can't get something for nothing," and that's true for refining processes.
Catalytic hydrocracking differs from others by using bifunctional catalysts, combining hydrogenation and cracking. It's exothermic, releasing heat while producing lighter, high-quality fuels from heavy feedstocks.
Unlike simpler methods, it requires careful impurity removal and offers flexibility in operations. While it's costlier, the high-value products and low-sulfur fuels it generates can enhance refinery profitability, making it worth the investment.
What Environmental Impacts Are Associated With Hydrocracking?
When you consider the environmental impacts of hydrocracking, you'll notice it generally has a lower global warming potential compared to alternatives like pyrolysis.
You'll also find its acidification and eutrophication potentials are significantly reduced.
However, while spent catalysts can pose toxicity concerns, they aren't classified as hazardous waste.
Are There Alternative Methods for Upgrading Fischer-Tropsch Waxes?
Yes, there are several alternative methods for upgrading Fischer-Tropsch waxes.
You can explore hydrotreating to enhance fuel stability or dewaxing to improve cold flow properties.
Selective catalytic cracking offers another route, while autothermal reforming is useful for syngas production.
Additionally, using zeolite-supported catalysts can effectively hydrocrack FT waxes.
Co-processing FT waxes with other feedstocks can also optimize efficiency and reduce emissions, providing you with versatile options for upgrading.
What Types of Catalysts Are Commonly Used in Hydrocracking?
In hydrocracking, you'll commonly encounter catalysts that feature metals like nickel, tungsten, and cobalt, often supported on acidic materials like zeolites or silica/alumina.
These bifunctional catalysts facilitate both hydrogenation and cracking reactions.
When sulfur's present, noble metals like platinum and palladium may be used, but base metals generally handle sulfur better.
Phonolite-supported catalysts, in particular, demonstrate improved resistance to carbon deposition, enhancing overall performance and stability during the process.
Conclusion
In summary, upgrading Fischer-Tropsch waxes into transport fuels through catalytic hydrocracking and isomerization opens a new chapter in sustainable energy. Imagine a world where clean, efficient fuels flow like a river, powering our vehicles while leaving a minimal carbon footprint. By harnessing these innovative processes, you're not just contributing to energy solutions; you're fueling a greener future. Let's embrace this transformative journey and drive towards a sustainable tomorrow, one drop of fuel at a time.